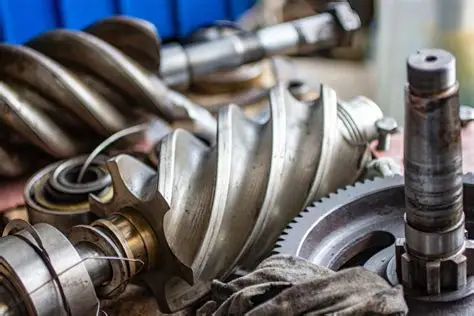
Neglecting timely maintenance of your rotary screw compressor can result in serious operational and financial consequences. Many businesses overlook routine service until something goes wrong, leading to major repairs, costly downtime, and even complete equipment failure.
The biggest cost of delayed maintenance is unplanned downtime. A failing compressor can halt production, affecting deadlines and client satisfaction. Emergency repairs are also more expensive than scheduled servicing. Replacing a damaged motor or internal parts costs significantly more than preventive tasks like changing oil or replacing filters. Energy efficiency also takes a hit. A poorly maintained compressor consumes more power due to clogged filters, low oil levels, or component wear. Over time, higher electricity bills significantly impact your bottom line. Additionally, component lifespan is shortened. Parts such as bearings, seals, and valves wear out faster when not properly maintained. This leads to more frequent replacements and increased maintenance budgets. The rotary screw compressor service cost effects can also extend to warranty issues. Ignoring service intervals voids manufacturer warranties, leaving you unprotected in case of major breakdowns. This can lead to full out-of-pocket expenses for repairs or replacements. Understanding rotary screw compressor service cost effects helps prioritize preventive maintenance. It ensures optimal performance, reduces unexpected expenses, and extends compressor life. To avoid unnecessary costs, stick to a strict service schedule. Preventive maintenance is an investment that saves your business money in the long run. Don’t wait for a breakdown. Explore our Rotary Screw Compressor Maintenance services or Contact Us today to schedule a professional maintenance check. For a complete care plan, visit our Screw Air Compressor Maintenance guide.